Program design and implementation
Changes across the utility industry are accelerating, from customer behavior to energy demand growth. We help utilities design programs that remain flexible and reliable amid disruption—using advanced data modeling and innovative technology solutions to unlock the possibilities of revenue growth, sustainability, and better customer and community outcomes.
Power reliability, strategy, and planning
Today’s utilities need to seamlessly transition to modern infrastructure, ensuring long-term cost savings and enhanced grid resilience. Our expert guidance empowers utilities to achieve reliable, affordable, and secure energy solutions by integrating cutting-edge technologies to build the grid of the future.
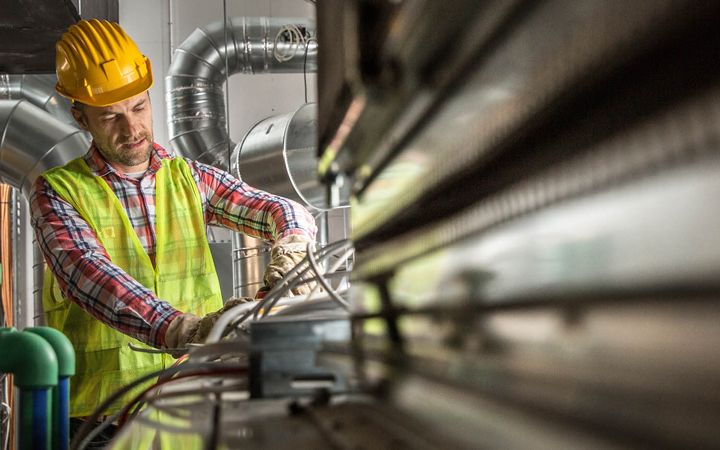
Integrated system planning
Our comprehensive solutions enhance coordination between GT&D processes, leading to optimized investments and improved reliability.
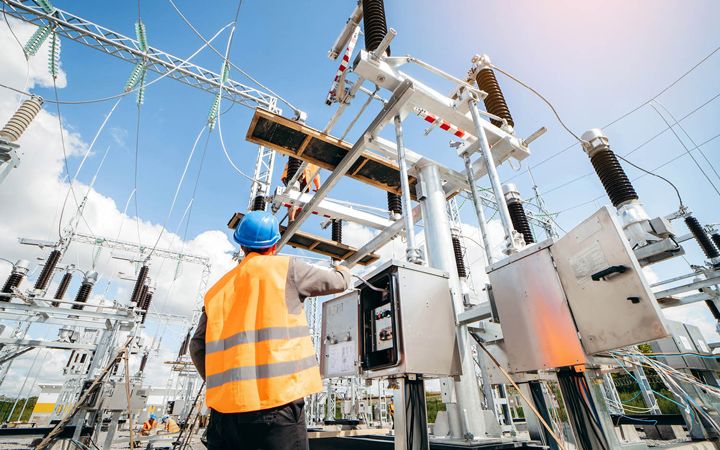
Energy resilience
Through tailored resilience frameworks, roadmaps, and stakeholder engagement, we help utilities reduce vulnerabilities and ensure reliable service.
Our services
Strategy and planning
- Demand management strategies
- Integrated grid planning
- Transmission and distribution systems planning
- Capacity planning
- Environmental impacts
- Energy access
- Target setting/road mapping
- Integrated Resource and Resilience Planning (IRRP)
- Utility resiliency strategy
- Regulatory support
Implementation and engagement
- Program implementation and support
- Marketing, outreach, and customer engagement
- IT platforms
- Customer insights and incentives
- Analytics
- Stakeholder engagement
- Regulatory compliance
- Rebate processing
- Call centers
- EM&V program optimization
Domain expertise
- Distributed Energy Resources (DERs)
- Renewables (wind, solar, battery storage)
- Oil, gas, power, and coal
- Non-wires / Non-pipes alternatives
- Flexible load management
- Load interconnections
- Reliability/Resource adequacy analysis
- Stakeholder facilitation
- Technology and innovation
Engineering
- Power system modeling
- Substation design
- Relay protection and analysis
- NERC compliance
- SCADA
Best-in-class support for energy project development and investment
Our strategic advisory services can also help you with comprehensive market analysis and forecasting, throughout the entire lifecycle of energy projects
Our work
Our insights