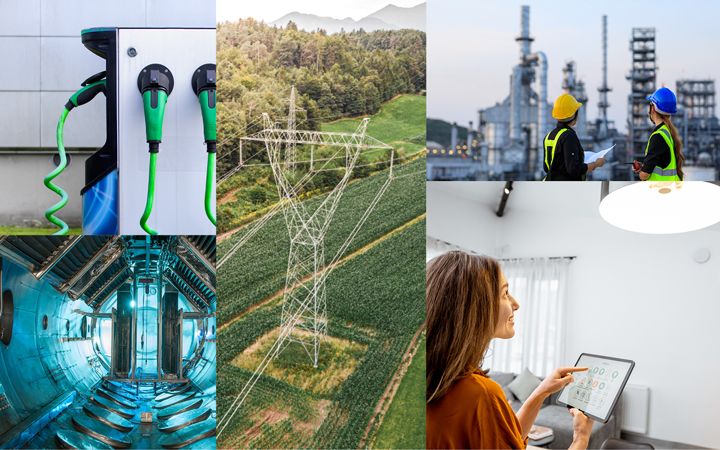
Comparing the costs of industrial hydrogen technologies
Hydrogen producers may need to decide whether to use steam methane reforming (SMR) or autothermal reforming (ATR) technologies. Understanding the maximum single train capacities for key equipment and systems can provide insight into why the different technologies may be employed at various plant capacities.
Maximum single train capacities for equipment and systems can significantly impact hydrogen production and capital costs. Here, we briefly discuss these technologies and how their costs are impacted by the planned hydrogen production scale.
There are also significant emissions associated with the use of natural gas in the production of hydrogen. With aggressive targets being set to reduce emissions by 2050 or earlier, and with large proven natural gas reserves, there is a risk that a significant portion of the natural gas resource will not be extracted and utilized.
Hydrogen production from natural gas with carbon capture and sequestration or CCS—sometimes referred to as “blue hydrogen” production—is one means of facilitating the continued use of natural gas in hydrogen production as the industry decarbonizes. Commercial scale hydrogen plants with CCS are currently operational with more plants under construction or being planned. These plants employ a mix of SMR and ATR, some at very large hydrogen production capacities.
This article aims to provide some insights into what factors go into technology selection for hydrogen production with CCS at various production scales, which can help optimize hydrogen production and capital costs while delivering the greatest return on investment.
Reformers
Steam methane reforming
A hydrocarbon feedstock (naphtha and lighter) can be converted into a synthesis gas (syngas) by reaction with steam inside of piece of standard industrial equipment called a steam methane reformer. The reformer contains metal tubes, filled with a nickel-based catalyst. The tubes are supported inside of a refractory lined firebox, where a large number of burners combust fuel to generate the external heat necessary to provide for the endothermic heat of reaction (Figure 1).
Figure 1: SMR configuration
A practical limit for the number of reformer tubes in a single box is approximately 1,000, with a common outside tube diameter of around six inches and a maximum practical tube length of 40 feet. A larger SMR box becomes too difficult to maintain the structural integrity of the enclosure without excessive additional bracing, stiffeners, and external structural steel. SMRs are typically field fabricated, especially when they have large capacities.
As approximately 60% of the SMR cost is associated with the reformer tubes and catalyst, which both scale fairly linearly with capacity, the capital cost of the SMR does not scale up to large capacities as economically as other equipment (e.g., refractory lined vessels).
A single SMR train is expected to have a maximum single train capacity equivalent to approximately 650,000 kg/d of hydrogen production. Above this capacity, multiple SMRs would be required. The single train systems are most often designed with a pre-reformer that converts all hydrocarbons heavier than methane into methane, hydrogen, and carbon oxides.
The reformer catalyst is impacted mainly by sulfur and carbon deposits that form over the normal course of the chemical reaction. To avoid carbon deposition on the catalyst, the steam-to-carbon (S/C) ratio at the inlet of the reformer tubes is typically controlled at above 2.5:1 (for natural gas feed). This results in a syngas with a H2:CO ratio above 3.0. Due to reformer tube life (creep) limits and reaction equilibrium considerations, the reformer outlet pressure is usually less than 450 psig. The outlet temperature is usually limited to 1650 degrees Fahrenheit.
For >90% carbon capture and sequestration (CCS) of CO2 in the SMR derived syngas and the SMR flue gas, it is possible to achieve plant lifecycle CO2e emissions approaching 4.0 kg CO2e per kg hydrogen produced.
Autothermal reforming
In an autothermal reformer, partial oxidation of the hydrocarbon feedstock is conducted, inside of the reformer vessel, to produce the heat required for the endothermic reforming reactions. External steam is added, but a lower S/C ratio of above 1.0 is feasible (for natural gas feed). The oxygen added to generate heat in the reactor is chemically bound in the product gas, which results in a lower H2/CO ratio in the produced syngas (~2.5:1). The arrangement inside an ATR, with the burner located above a catalyst bed, is illustrated in Figure 2.
Figure 2: ATR configuration
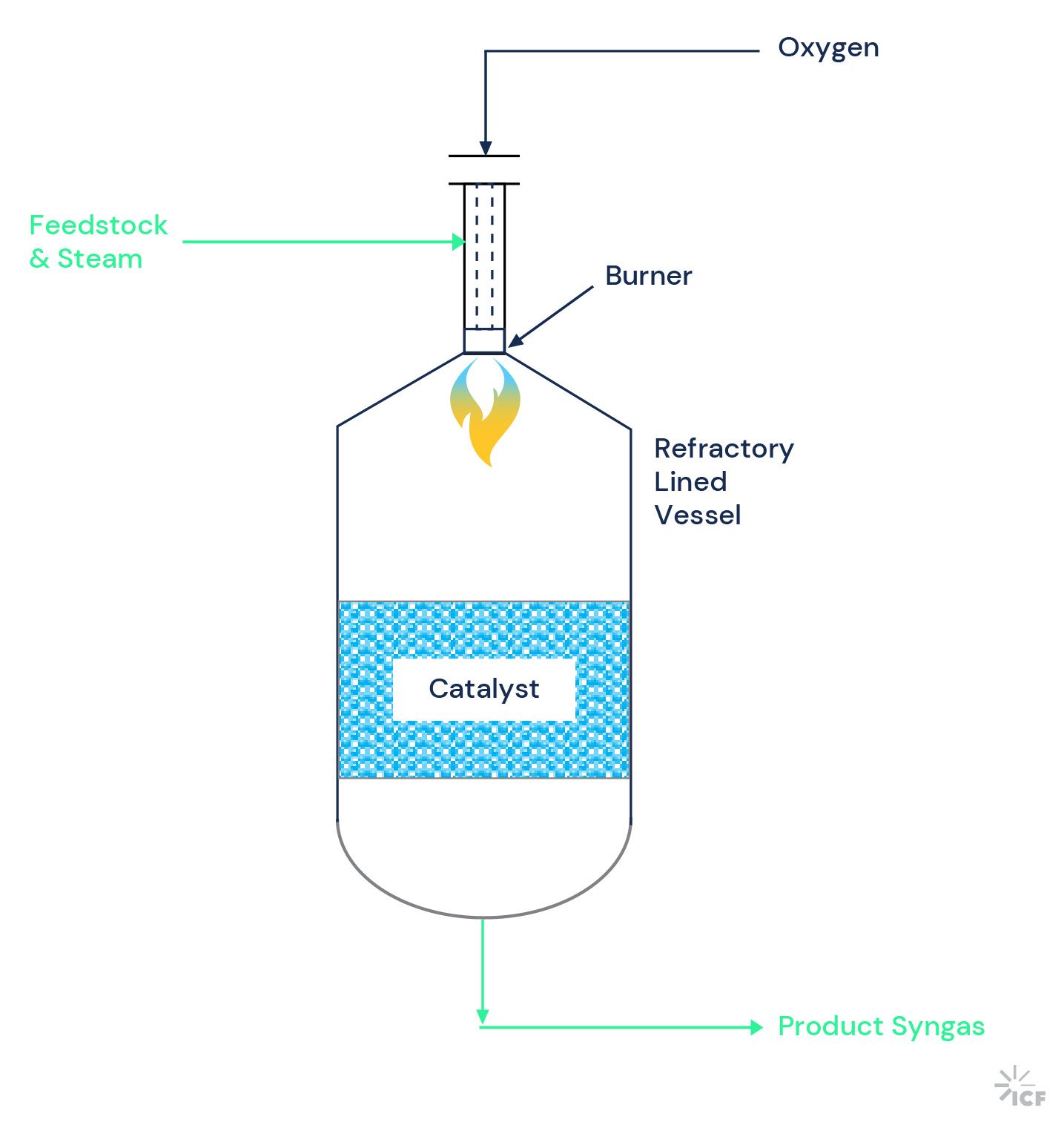
ATR exit temperatures are usually less than 2000 degrees Fahrenheit, and the operating pressure is usually less than 600 psig. A pre-reformer can also be used upstream of the ATR, as described above for the SMR. Typically, a feed furnace is included in the flowsheet to heat the pre-reformer feed.
An ATR vessel with a refractory internal diameter of approximately 23 ft (shell diameter approximately 26 ft) is technically feasible. The ATR vessel would normally be shop fabricated, so limitations in the size of vessels that can be transported to the project site could also potentially limit the maximum single train size. Assuming no transport limitations—and an operating pressure of 400 psig, suitable for hydrogen production—a maximum single train capacity for an ATR would be equivalent to a production rate of approximately 1,100,000 kg/d H2.
The capital cost of the ATR reactor scales up to large capacities more economically than SMRs, due to its significantly simpler construction.
The ATR based hydrogen plant is typically more thermally efficient than the SMR based hydrogen plant but has a significantly higher parasitic power demand. This is due primarily to the incorporation of an air separation unit (ASU) in the plant, to provide the oxygen required for the ATR.
Although the CO2 capture in the ATR derived syngas is typically high (>90%), there is normally a requirement for a fired heater to preheat the feed to the ATR Reactor or pre-reformer which will result in more emissions, unless this CO2 is also captured.
Partial oxidation (POx) reactor
The POx reactor is essentially an ATR reactor vessel without the catalyst bed. To achieve the desired hydrocarbon conversion in the POx reactor, the operating temperature is significantly elevated (typically above 2500 degrees Fahrenheit), in addition to providing sufficient gas residence time (several seconds). Because the POx reactor does not contain any catalyst the process is extremely feedstock flexible, which is the major advantage of the POx system over the SMR and ATR. As the analysis provided below is for natural gas feedstock only, POx based hydrogen plants have not been included in the subsequent analysis.
Capacity limitations of other major equipment in hydrogen plants
Air separation units (ASU)
A “single stream” ASU design is technically feasible for a 5,000 metric tonnes per day (MTPD) oxygen plant. In this case, the MAC (main air compressor) and BAC (booster air compressor) drive power is expected to be approximately 90 MW and at least one drive vendor has a reference for that size drive. Currently the largest single train ASU in the world is rated to produce 5,000 MTPD oxygen.
The largest single train ATR based hydrogen plant (1,100,000 kg/d H2) would require approximately 5,100 MTPD of O2, so it would (just) be within the capability for a single train ASU. In some cases, the plant owner might prefer to target a maximum ASU capacity of approximately 3,500 MTPD, which is more commonly deployed commercially and makes several more compression and drive solutions available—and could also improve the unit costs for the ASU.
Water gas shift unit
Radial flow shift reactors allow for very large single train reactors to be designed for an application. The number of water gas shift reactor trains can generally be matched to the syngas generation technology.
CO2 removal
The limit for the maximum single train capacity for the CO2 removal unit will depend on the technology selected in this application and the hydrogen plant configuration. In general, the cost (and weight) of large diameter, very tall, high-pressure trayed and/or packed absorber columns limits the economic single train capacity at approximately 650,000 kg/d H2, for both SMR (syngas and flue gas CO2 capture) and ATR based (syngas CO2 capture only) plants.
CO2 compression
Although very large single train CO2 compressor packages (> 20 MWe) are technically feasible, for this analysis we assumed a maximum single train CO2 compressor rating of 16 MWe to make more compressor solutions available. Hence for an SMR or ATR based hydrogen plant, depending on the CO2 pipeline pressure required, a single train CO2 compressor (ignoring redundancy) might be achievable for up to a 500,000 kg/d H2 plant capacity.
Pressure swing adsorption (PSA) unit
The maximum size achievable for a single train PSA unit is generally limited—at approximately 650,000 kg/d H2—by the size of the switching valving that can be purchased for the application.
Analysis
With the maximum single train capacities as discussed previously, it is possible to determine the capital cost and hydrogen production costs for an SMR and ATR based plant, with CCS, at a range of H2 plant capacities. Capital costs include carbon capture and compression but exclude pipeline and sequestration costs. This analysis is summarized in Figure 3 and Figure 4:
Figure 3: H2 plant capital costs
Figure 4: H2 production costs
The SMR and ATR based hydrogen plant capital costs are similar at the lower end of the capacity range considered in this analysis (150,000 kg/day or 62.5 MMSCFD H2). However, the SMR based hydrogen plant’s capital costs increase above the ATR based plant costs as the plant capacity is increased above this minimum capacity. Part of the cost difference is attributed to the less economic scale up of the SMR versus the ATR reactor. In addition, at 650,000 kg/d H2 (270 MMSCFD), the SMR based H2 plant costs step up significantly, as the single train capacity limits for the SMR, CO2 removal units—including for the expensive flue gas CO2 capture unit—and the PSA units are reached simultaneously.
The ATR based hydrogen plant experiences a significant cost increase at approximately 750,000 kg/d H2 (312 MMSCFD H2) if the ASU maximum size is constrained at 3,500 MTPD O2, at which point a second ASU train would be required.
The SMR and ATR based hydrogen plant production costs are similar at the lower end of the capacity range considered (150,000 kg/day or 62.5 MMSCFD H2)—although the slightly lower ATR based plant capital cost and higher thermal efficiency more than compensates for the higher power costs for this case, resulting in a slightly lower cost of hydrogen production for the ATR based plant at this lower capacity. Note that this production cost difference is highly dependent on the assumed power price (we used $60/MWh in this analysis), which will be variable depending primarily on the plant location.
In our analysis, this relatively small cost delta is more or less maintained up and until the threshold capacity of 650,000 kg/d H2 (270 MSCFD H2) is reached. At this point the ATR based hydrogen plant production costs become significantly lower, primarily due to the capital cost increases that occur for the SMR based H2 plant at this threshold capacity, as discussed above.
The ATR based hydrogen plant experiences a significant production cost increase at approximately 750,000 kg/d H2 (312 MMSCFD H2), if the ASU maximum size is constrained at 3,500 MTPD O2, at which point a second ASU train would be required with the associated capital cost impacts. The ATR based H2 plant, however, still produces hydrogen at a lower cost than for the SMR based plant at and above this capacity—even with this lower ASU maximum single train capacity constraint.
Our analysis concludes that ATR based hydrogen production plants generally produce hydrogen at a lower cost than SMR based plants, except for smaller capacity plants and/or where power is more expensive. Note that potential availability benefits associated with multiple equipment and system trains were not analyzed as part of this study but could be included in a future analysis.